【导语】作为钢铁冶炼的主要原料,废钢铁在不同生产工艺中扮演的角色也有所不同,因此在不同的生产工艺下,吨钢生产的能耗以及碳排放也存在一定的差异。本文将重点梳理不同生产流程下的吨钢生产能耗以及碳排放,分析未来废钢铁在钢铁冶炼中的应用变化。
废钢铁在长流程和短流程冶炼中扮演的角色存在较大的差异,在长流程中更多是起到辅助的作用,而在短流程中则是主要铁元素供给原料。因此在不同的生产工艺下,吨钢生产所需要的原料便存在较大的差异,根据北京科技大学朱荣教授在《电弧炉炼钢成本分析及降成本研究》中物料平衡的计算,不同生产工艺吨钢生产所需的原材料如表1所示:
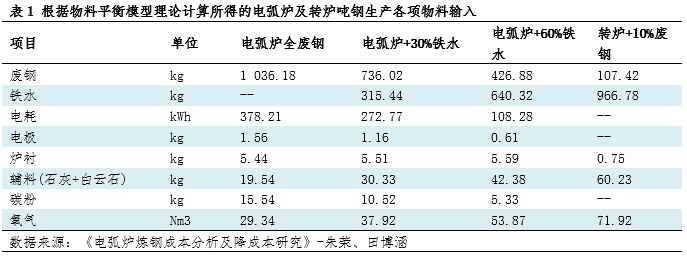
从铁元素供给总量来看,由于铁水中其他元素(主要是C)含量较高,在冶炼过程中可能存在较大的烧损,所以废钢+铁水的铁元素供给总量与废钢比呈反比,随着废钢比的提高,铁元素供给总量会有所下降。而从能耗方面看,电弧炉全废钢冶炼的能耗较30%废钢冶炼能耗高约39%,较40%废钢冶炼能耗高249%。可见对于电炉来说,废钢添加的比例越高,能耗成本也会随之上升,辅料方面电极的消耗也会增多。而对于辅料以及氧气的需求也与废钢投入成反比,随着废钢比的提高,辅料和氧气的使用也会有所下降。
当然,在此一定有人提出质疑,添加的铁水不需要能耗吗?必然也是需要的,因此对于不同冶炼情况下的能耗计算冶金工业信息标准研究院的相关专家也给出了相应标准,短流程以电炉冶炼能耗加对应铁水能耗,长流程则是在不同废钢比下的能耗。具体如图1所示,整体来看,不论是长流程炼钢还是短流程炼钢,随着废钢使用比重的增加,能耗均会有所降低。当废钢使用比例小于40%的时候,长流程炼钢的能耗要显著小于短流程,但是由于长流程炼钢工艺的限制,转炉里添加废钢的比例区间范围有限,相反电炉则可以实现100%全废钢冶炼,因此当废钢使用占比超过50%的时候,电弧炉的优势才可以得到充分的发挥,能耗可以显著小于40%废钢比的长流程炼钢。
在钢铁行业进行绿色低碳转型的过程中,除了需要关注低能耗外,更需要关注的就是碳排放量的多少。其中,短流程电炉中的原料比例主要是废钢和铁水,因此在计算碳排放的时候对这两种原料进行分别计算。即短流程炼钢碳排放量=电炉冶炼碳排放+铁水生成碳排放量。而长流程炼钢的碳排放量则需要根据添加的废钢比进行相应的计算,大体公式可以为:碳排放量=铁前工序碳排放量-转炉冶炼工序节省的碳排放量。因此不同生产条件的二氧化碳排放如图2所示。整体来看随着废钢比的增加,碳排放均呈现了一定的下降趋势,而且与能耗变化类似,当废钢比小于40%的时候长流程占据优势,当废钢比超过50%的时候,电弧炉炼钢的优势才能得到很好的体现。
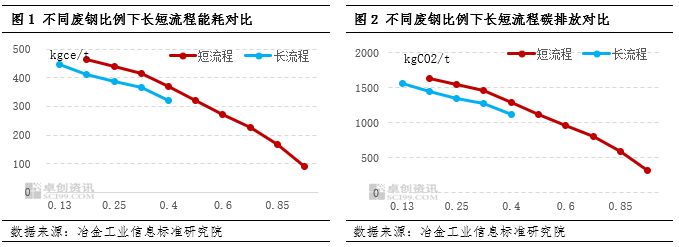
综上可以看出,在钢铁行业的绿色低碳发展过程中,并不是要一味的舍弃高炉冶炼完全转向电弧炉冶炼,反而是要发挥不同冶炼方式的特点,实现“双碳”目标。因此未来废钢铁的发展大致会逐渐形成两种方式,第一是鼓励电弧炉发展全废钢冶炼。这对废钢的料型以及资源供应量等会有着更高的要求,此外合适的价格也是实现这一目标的必要条件,不然就会为了“绿水青山”而舍弃了“金山银山”;第二是长流程钢企尽可能的提高转炉废钢比。目前长流程仅通过采取提高废钢比的措施,仍有较大节能减碳空间,废钢比达到20%~30%左右,理论计算可较当前水平实现节能减碳8%~18%左右。